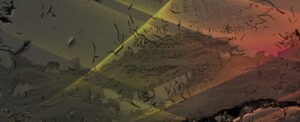
SHARE
Grace Under Pressure
- By: Levi Hawkins, PE, Director of Project Management
Blazing the Trail of Large Diameter Pressure Pipe Rehabilitation in the U.S.
Let’s take a walk in the early 2000’s. Flip phones, Harry Potter, and reality TV, a time when social media meant actually taking part in society. The early 21st century also saw an extreme rise in housing production with 2.3 million homes built in 2005, slightly below the all-time high set in 1978. Across the country developers were struggling to keep up with the demand of the American housing market. Equaling that growth was the required infrastructure such as roads, electrical lines, gas, sewer, and water utilities.
Arizona was no stranger to the expansion. Unlike never before the outskirts of Phoenix were becoming cities all their own and the development of major roadways meant commuters no longer needed to reside in the metropolitan area. From 2000 to 2010, the city of Maricopa, once a “blink and you’ll miss it” town for Phoenicians to pass on their way to southern California, grew from a population of under 2,000 to over 40,000 residents. To stay ahead of the growth, contractors built the necessary infrastructure to serve the future residents of the city. Miles of pipe was laid across the city with the expectation that housing developments would soon be tied in. The only thing that could throw a wrench into the plan was the worst financial crisis since the great depression.
Fast forward to today. Housing demand is as high as it’s been in decades, infrastructure once placed for growing cities is now being called upon to serve long-awaited residential communities. The demand for pipelines built 20 years ago was finally realized, and it was time to test their integrity and engineering design. Naturally, there were problems.
The subject of this article specifically is a 24-inch potable water pipeline in Arizona. Built in the early 2000’s and laid rest until recently called upon to serve the community. The problem? The pipeline was pressure tested again and again but simply would not hold. The rushed nature of construction and engineering, and the typical stresses of earth pressure and loading resulted in two, 100-ft long segments of leaky pipeline. In other similar circumstances, a city may cut their losses and simply remove and replace the pipeline. In this case, the pipe happened to navigate above and below major utilities. Namely a large irrigation channel serving the agricultural districts in the area, and one that could not be disturbed without major coordination and permitting. As if that wasn’t enough of a challenge, the pipeline happened to be within multiple jurisdictions making removal and replacement a feasibility and bureaucratic nightmare.
Until 2022, pressure pipeline rehabilitation liners were limited to a maximum of 20-inch diameter. For a pipe designed to serve a large and ever-growing community, reducing to 20-inch was not an option. Coincidentally, CPM Pipelines launched the BulletLiner System® only months prior to the need to activate the 24-inch diameter waterline. The system consists of rugged, flexible fabric-reinforced pipe (FFRP) liner and specialty termination fittings. The liner can withstand triple digit internal pressures with ease, is corrosion resistant, and carries a useful life greater than or equal to conventional pipeline materials.
The stars aligned to not only avoid costly dig-and-replace construction, lengthy permitting processes, and eliminate capacity reduction, but to be the first of its kind large diameter pressure pipe rehabilitation project in the US. Thanks to the forward-thinking decision makers on the project team, history was made in what was once a small town on the outskirts of Phoenix.
Of course, this is no fairytale; the project was not without its challenges. The material characteristics of the rehab liner may have been unique, but the constructability issues were all too common for pipeline professionals. Record drawings? Not so much. Depth of cover, deflection angle, existing utility information? Equally scarce. In comes engineering judgement, which is just a fancy way to say guesstimating. The limited information available was used to approximate the length of liner needed, the position of the various pipeline bends, and the most effective locations for trenching to expose the pipeline.
Planning is a necessary and critical phase of any construction project, but the execution is where the rubber meets the road. In the end, the four excavation pits (two per rehab segment) were bullseyes. Additional coordination, permitting, and waiting was avoided by maintaining the digs inside the proper jurisdiction. The pits also landed outside of the various bends, leaving enough horizontal pipe in the trench to comfortably install the liner and termination fittings. Perhaps the biggest test for the lining phase was the ability for the BulletLiner System® to not only navigate the alignment changes, but fully open to its circular shape when inflated inside the host pipe. With little nail-biting, it did.
Applications exist in which removing and replacing a pressure pipeline is the most practical method, including increased capacity demand and a high number of tees, taps, or appurtenances. However, when rehabilitating a pressure pipe with an FFRP liner is feasible, one is hard pressed to find a more effective solution. In the case of the 24-inch waterline in Arizona, the savings in time, money, and public impact allowed a problem to be solved in weeks rather than months, and for the community to continue its prosperous growth.
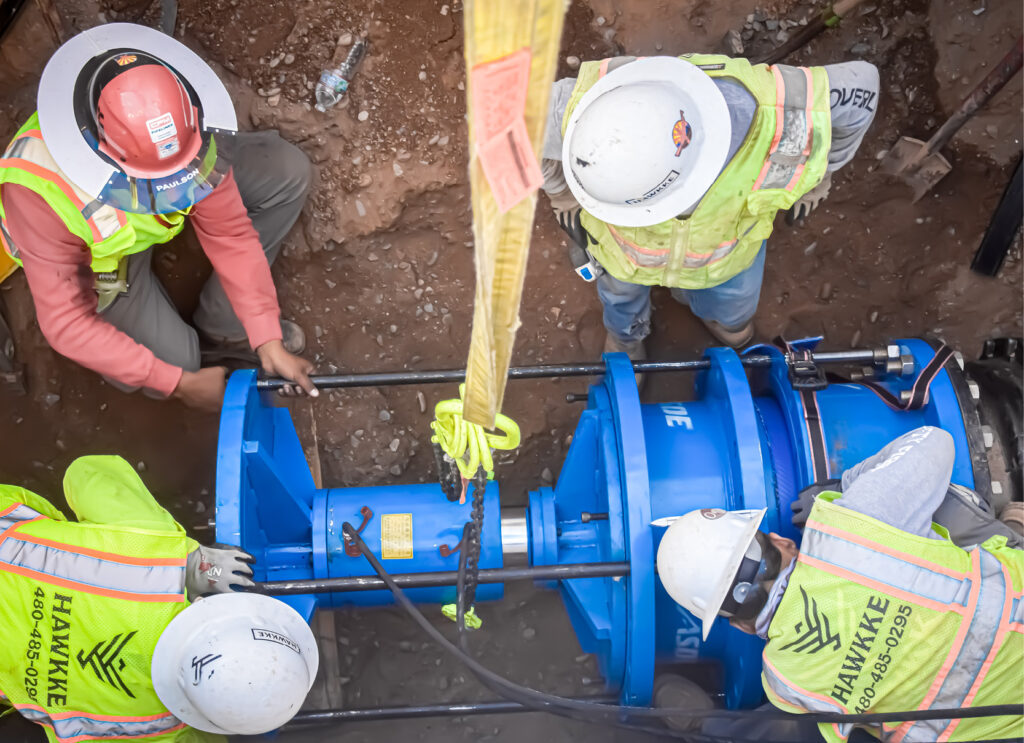


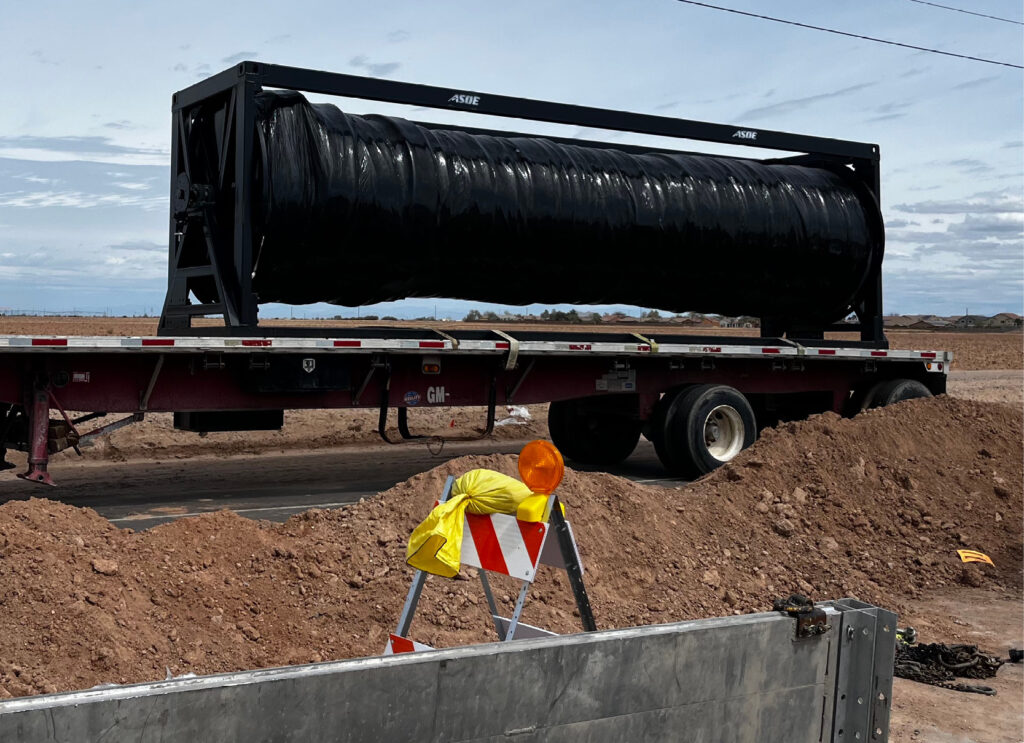