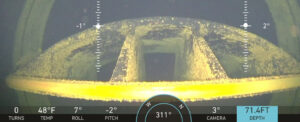
The Butterfly Valve Mystery
CPM’s recent project with a water utility client captured amazing footage providing a simple explanation for the (considered) inconsistent data captured through the client’s modeling software.
CPM was contracted to perform a phased pipe condition assessment utilizing INGU Pipers® free floating, pre-screening inspection tools, Electromagnetic Bracelet Probe™ (BP) scanning, and Ultrasonic Thickness (UT) measurements on two wastewater force main pipelines. One 16-inch asbestos cement (AC) line, and one 16-inch ductile iron (DIP). CPM also performed an inspection of the existing air release valves (ARVs) along the pipelines between the inspection limits.
According to as-built records provided by the owner, the AC and DIP pipelines were constructed in 1972 and 1989, respectively. The multi-phase inspection and condition assessment efforts were performed over a three month period. The process of determining the condition of the pipelines began with an in-line Pipers® survey to determine areas of degradation by locating gas pockets. After establishing these locations, a more focused analysis was performed to provide tangible data that can be used to establish a baseline condition of the focused locations and understand remaining useful life, and provide recommendations for repairs. The pipelines were non-destructively inspected using the following techniques, in order:
Each subsequent step of the process provides greater detail of the most concerning sections of the pipeline. Ultimately, precise measurements are taken from which conclusions and recommendations are provided. Note that the AC PipeScanner serves as the final step for AC pipe as the tool provides immediate thickness data without the need for ultrasonic thickness testing. A description of the tools used, and processes performed for each of these steps is provided in the following section of this report.
Like the DIP condition assessment, after the Pipers® detect areas of concern along the AC pipeline a specialized tool is used to precisely locate spots of degradation. For AC pipe CPM utilizes the AC PipeScanner by Acquaint. Like the Bracelet Probe, the PipeScanner (shown in Figure 1) allows the user to detect structurally degraded areas of pipe wall using ultrasonic transducer technology. The UT sensor within the PipeScanner unit is coupled to the pipe wall with water to allow the signal to pass easily to, and through, the pipe wall. The tool is manually passed over the pipeline while it records thickness data according to portions of the pipe that have lost structural strength. As it is moved, a constant stream of water is introduced at the sensor. Scans are completed at a rate of several feet per minute and the tool moves longitudinally in the direction of flow. When one scan is complete, the tool is moved to the next clock position and another scan is performed. When the desired number of scans are taken, the PipeScanner is simply hooked up to a laptop computer and the data is transmitted for interpretation and reporting.
The AC PipeScanner does not simply measure the thickness of the pipe wall from outside diameter to inside, like the BP. Instead, the PipeScanner measures thicknesses within the overall pipe wall where structural strength has been compromised due to leaching of chemicals of the original material makeup, such as lime.
The full data output from the PipeScanner is shown in Figure 2. The graph shows the span of wall thickness measurements taken and notes have been added to aid in the interpretation of the results (clock positions are assigned as if facing toward the downstream end of the pipeline). For example, the scan carried out along the 1 o’clock position had an average, remaining structurally sound wall thickness reading of approximately 0.475-inches, a minimum of 0.380-inches, and a maximum of 0.525-inches.
A test scan is performed before true data is taken to ensure the equipment functions as expected and that the results are consistent with the pipe material, age, and diameter.
As with the ductile iron pipeline, the results indicate that the AC pipeline has also undergone severe wall loss. According to prior communication, the wall thickness of the AC pipe at the time of installation was approximately 0.73-inches.
It was previously stated that wastewater pipeline degradation is typically most severe at the top portion of the inner pipe wall. As a testament to this trend, Figure 2 denotes substantial wall structure loss from the 10 to 3 o’clock positions of the section of AC pipe that was scanned. Based on the information gained with the AC PipeScanner tool, the most severely deteriorated sections of pipe were found to have experienced roughly 50% structure loss (10 and 11 o’clock position specifically). The remaining clock positions that were scanned were not much better, ranging from as much as 40% loss (2 and 3 o’clock positions) to the low end of about 30-35% loss (1 o’clock position). The loss of wall structure is caused by leaching of calcium within the pipe wall, resulting in a reduction of tensile strength.
For each of the inspection tools used, CPM provides the data from Phase 2 (BP and AC PipeScanner) to the equipment manufacturer and receives general feedback and confirmation of the findings. While CPM has extensive experience in data collection and interpretation with the tools, manufacturer opinion strengthens confidence in the findings and occasionally eliminates false-positives or isolated, unusual results (although none such discrepancies were noted in the case of these pipeline assessments).
CPM performed BP scanning, UT testing, and AC pipe scanning for two 16-inch wastewater force main pipelines – one ductile iron and one asbestos cement. CPM inspected what is typically the fastest area of the pipe to degrade (verified air pocket locations along the top portion of the pipe wall) and found that each pipeline was severely deteriorated. Precise data was obtained on only short portions of the pipelines; therefore, any conclusions can only be applied to these specific sections of the pipeline.
Assuming class 350 DIP, the design pressure of the pipeline at the time of manufacture was approximately 1,640 psi.
Using the minimum wall thickness value gained during the UT testing of the DIP line (0.155 inches), the current, safe maximum operating pressure for the inspected section of the pipeline is approximately 748 psi. The maximum operating pressure determined during the Pipers® investigation was 55 psi. However, pressure surges associated with functions of the associated pumps can exceed that value.
Asbestos cement pipeline design is much less straight forward. Pipe suppliers provided specific design and operation parameters based on the mode of manufacturing, pipe diameter, and pressure class. The design parameters for the 16-inch AC line are unknown, yet with engineering judgment and the data gained from this assessment effort dictate that the severity of degradation of the inspected area is similar to that of the DIP section. Formal calculations for estimating allowable pressure or remaining useful life are not readily available for AC pipe but there are further options for analysis of the pipe.
CPM’s recent project with a water utility client captured amazing footage providing a simple explanation for the (considered) inconsistent data captured through the client’s modeling software.
CPM was contracted to perform a condition assessment inspection along two sections of 8-inch ductile iron pipe (DIP) waste activated sludge lines located in Arizona.
Protecting human divers one Deep Trekker PIVOT inspection at a time. How a subaqueous swimming CCTV inspection solved the unknown in a 48-inch, potable water, intake pipeline 600-feet below.
An Arizona suburb pursues a long-term program to identify and locate leaks across its potable water pipeline system.
How one North Texas city is using new technology to protect its constituents from unforeseen water outages and loss.
Blazing the trail of large diameter pressure pipe rehabilitation in the U.S.